I started the day off cutting the torque tube collars to size
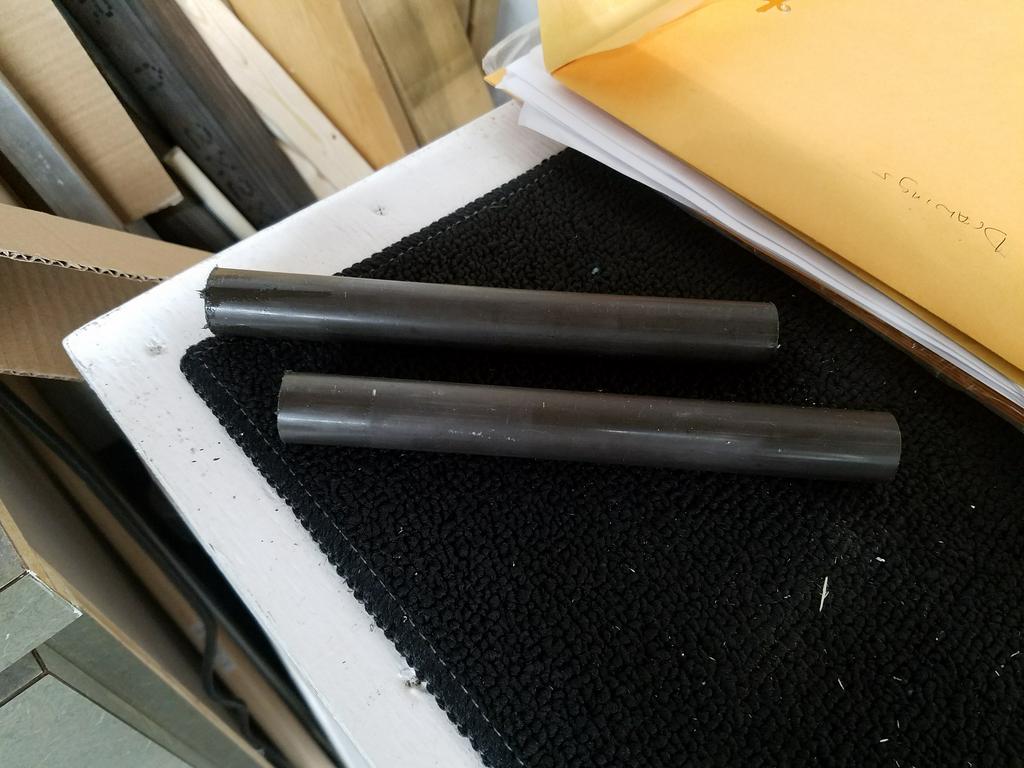
Then I match drilled the collars to the torque tube brackets
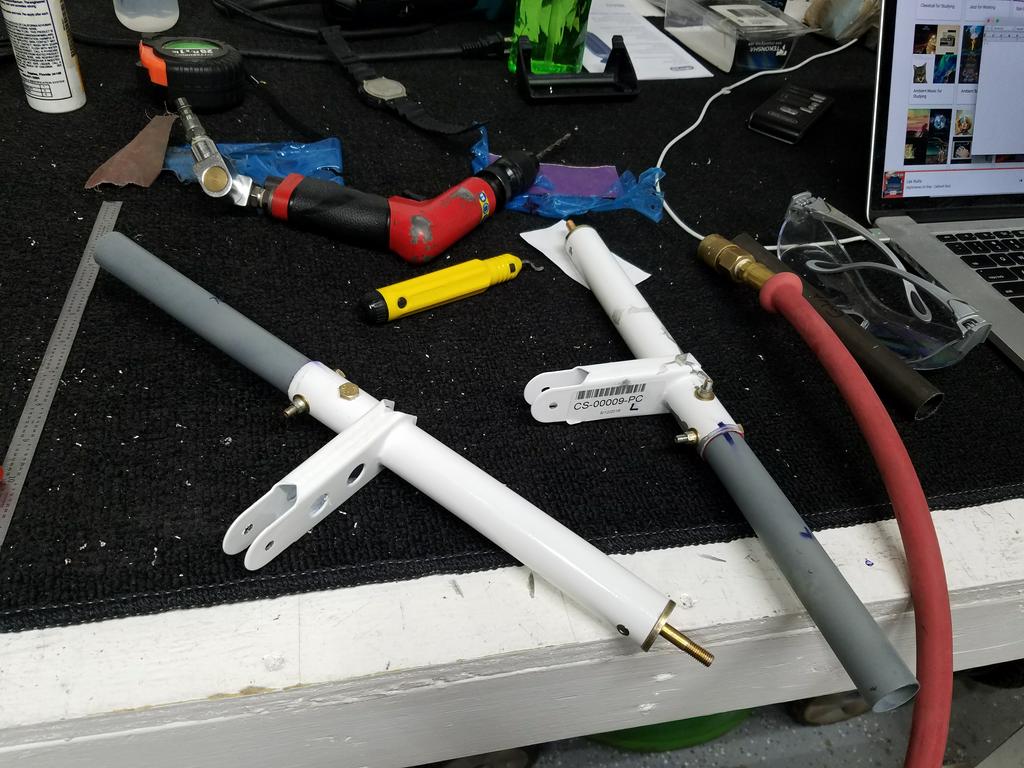
For the next drilling operation I had to create a spacer block with an exact dimension. So I decided to mill it on the milling machine
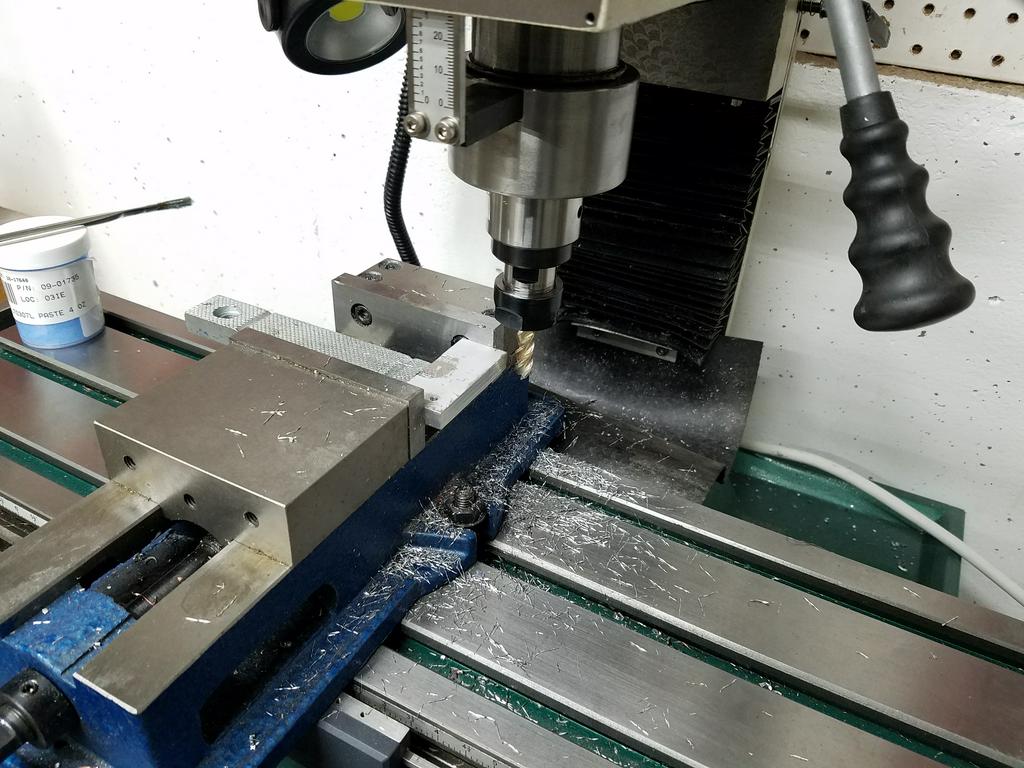
Hit by dimension (1 1/64") right on to within .0005"
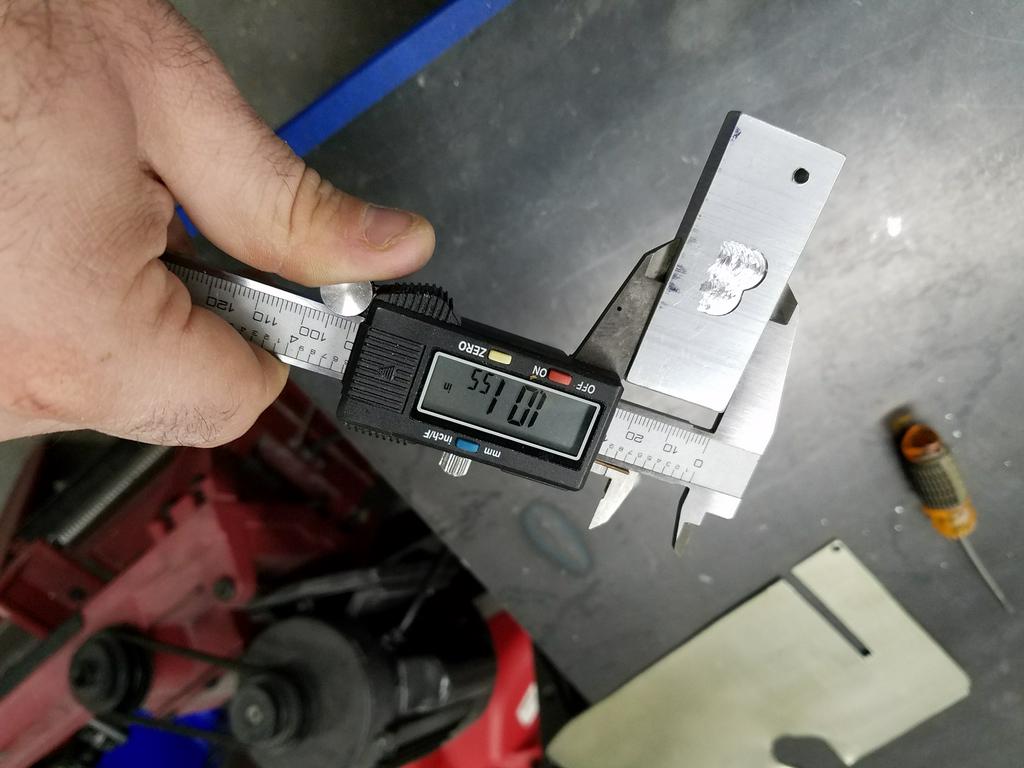
Then I had to drill the torque collars to the other torque tube sub-assembly. The length the final assembly makes is called out in the plans. So I drew lines on the table the appropriate length and then used 1-2-3 blocks to help line up the ends of the assembly. Then it was time to drill.

After I drilled out the holes in both asemblies I realized I had made an error in how I was measuring the overall length. So I had to re-setup and drill the holes again. I have 4 extra holes in the torque collar now =(. There shouldn’t be any structural problem with it, but I’m gonna call Van’s on Tuesday just to confirm. Otherwise I’ll have to order some new pieces of 4130 and do it all over again

Here are the assemblies bolted into the wings. There is some run-out on the left wing that is causing some flexing of the aft bearing bracket. I’m going to have to trouble shoot tomorrow and try and figure out there it’s coming from.
